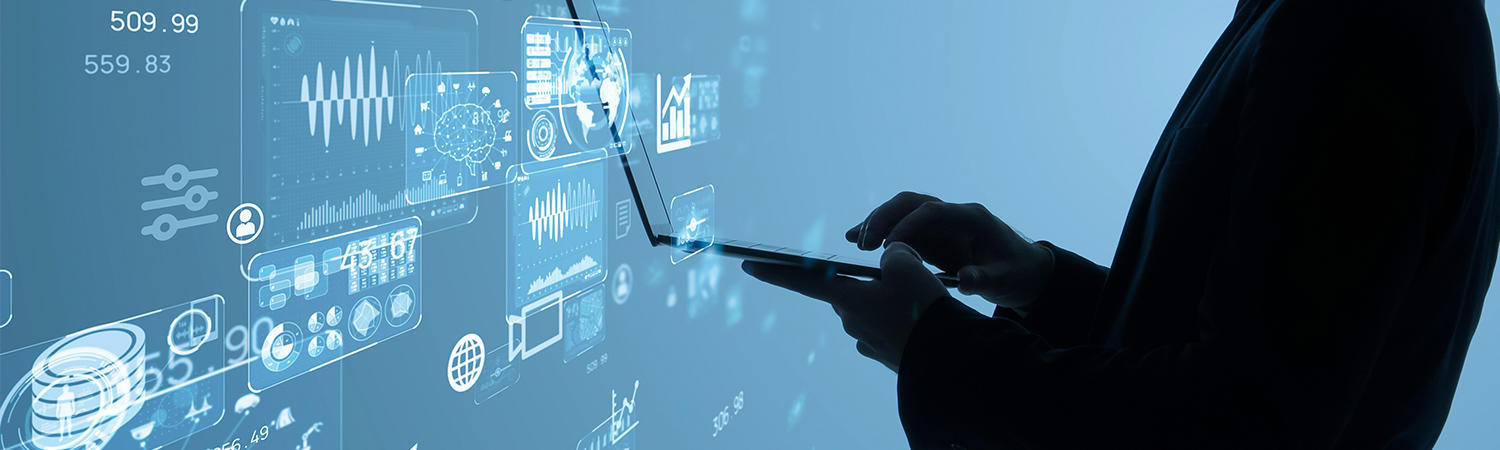
生産プロセス革新の実施
当社では、デジタルサポートによる生産プロセスの革新を進め、ものづくり力強化の加速(Smart Factory)とVirtual One Factoryの実現により、生産性の向上と工場間接工数の半減に向けて活動を実施しています。
デジタルサポートによる、ものづくり力強化の加速(Smart Factory)
生産プロセスのリアルタイムな稼働情報を生産管理のデジタルプラットフォームに集約することで、様々な改善、省人化に活用し、スリムな生産現場を構築します。
今後、2023年度までにモデルラインを構築していきます。その後、国内展開を進め、2025年度にはグローバル展開を目指します。
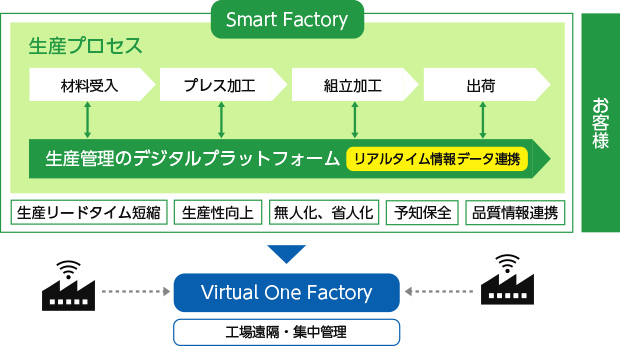
Virtual One Factoryの実現
生産現場でのデータ連携により、生産の管理や間接業務の遠隔、集中管理が可能となります。
2025年度を目標に拠点ごとの管理業務を国内1ヵ所で集中管理し、間接業務工数の削減を目指します。
取り組み事例
Smart Factory
-
生産リードタイムの短縮
生産指示情報の伝達をリターナブルかんばんから、データ転送に切り替え、かんばんの運搬や仕分け作業を無くすことで、生産から出荷までの情報の滞留を減らし、生産のリードタイムを短縮します。
-
無人化・省人化
誘導レール設置不要な無軌道走行式のAGVを採用し、導入を加速させます。生産進捗と連動した、完成品引き取り、部品供給を行い、部品運搬作業の無人化を進めます。
生産性改善加速
-
生産実績や停止要因を生産設備信号から自動取得することで、リアルタイムに生産状況を把握し、異常に対し迅速に対策と改善を実施し、生産性を向上させます。
また、タイムリーな生産情報を各種情報と連携させて、生産管理のデジタルプラットフォーム構築を進めていきます。 -
Virtual One Factory
生産管理業務の一極化
- 遠隔地からも現場の状況をリアルタイムに把握できるようにすることで、各工場で行っている工務業務を一極化し、全工場を一つの工場として管理します。これにより、管理工数の削減を進めます。
-
開発プロセス変革の実施
当社では、従来の各工程のバトンタッチ型開発から、製品、設備、工場の3Dデータを利用し、デジタル空間上で同時進行でアジャイルに開発するプロセスへの変革を進め、開発リードタイムの半減に向けて活動を実施しています。
開発プロセス変革の全体像
製品・設備の3Dデータのデジタルプラットフォームを構築し、開発から量産まで、3Dデータ上で情報の連携を行います。
また、3Dデータを用いたシミュレーション開発を充実させ、実製品データのフィードバックも活用し、開発の早期化、手戻りの低減を進めています。
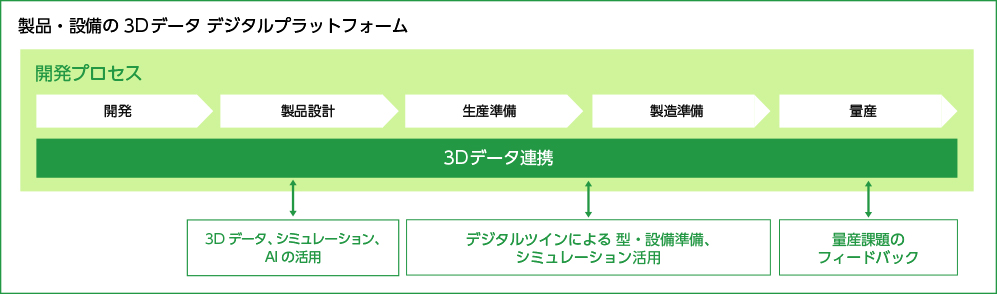
取り組み事例
製品設計にAI導入
従来、図面等の書類で行っていた製品設計後の生産準備指示は、3Dデータでの連携に移行しつつあります。当社では、3Dデータを軸にして、製品設計のプロセス見直しに取り組んでいます。その最適プロセスや設計ノウハウ、過去の知見等を学習したAIを導入し、設計者が着目すべきポイントに気づきを与える設計ガイドとして活用しています。設計品質のバラツキをおさえることにより、やり直しを防止し、製品の形状決定の早期化に貢献します。
生産準備にシミュレーションを活用
-
工場全体のレイアウトをデジタル空間に再現することにより、工場内の物流検討にシミュレーションを活用しています。
デジタル空間で運搬ルートの可視化や最適化、スペース等の事前検討を行い、設備搬入後の生産現場での製造準備工数の削減や量産開始後の構内物流の省人化に貢献しています。 -