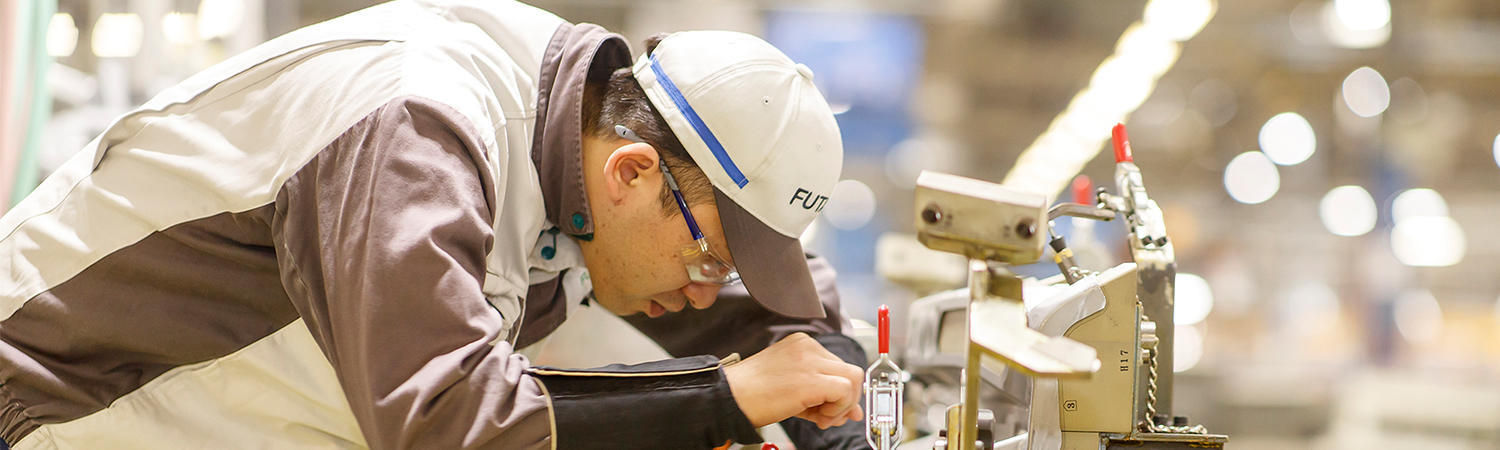
Basic approach
By setting quality assurance rules as a foundation in the works involving product planning and product inspection, we defined the objective and the responsibility of each job, making each department assume responsibility for quality assurance. Based on quality assurance rules and following the S-D-C-A* daily improvement cycle to gain the trust of customers, we are striving to improve our quality assurance systems with an emphasis on processes. We will also make a company-wide effort to enhance the quality assurance system by developing human resources capable of performing operations with a sense of ownership through work quality improvement activities based on the concept of total quality management (TQM). In addition, we allocate personnel on a priority basis to our quality assurance unit to identify quality-related risks from the initial stages of product development to the manufacturing process. Furthermore, we are focusing on the use of digital transformation (DX) to organize past failure information and provide feedback to the initial stage of product design.
* S-D-C-A: An acronym of standardize, do, check, and action.
Strengthening the quality assurance promotion system and governance
In April 2024, we launched the Quality Management Center, which consolidates organizations for quality assurance, quality audits, quality technology, and quality control department of the production plant into a single division. From the perspective of global quality assurance from the planning and design development stages, we will promote prevention activities incorporating countermeasures in the presumption of certain quality risks, thereby further ensuring quality assurance for customers. During audits, in addition to the QA inspections that have been conducted in the past, we are also conducting detailed and careful interviews with concern to psychological safety, such as whether or not there is an open workplace environment and culture. Specifically, we seek to determine if workplaces allow personnel in development and evaluation divisions, such as engineering and production engineering, as well as those in production divisions to speak out about any problems, whether or not excessive pressure is applied, and whether or not evaluations are made on a subjective basis, in order to investigate and respond to potential risks.
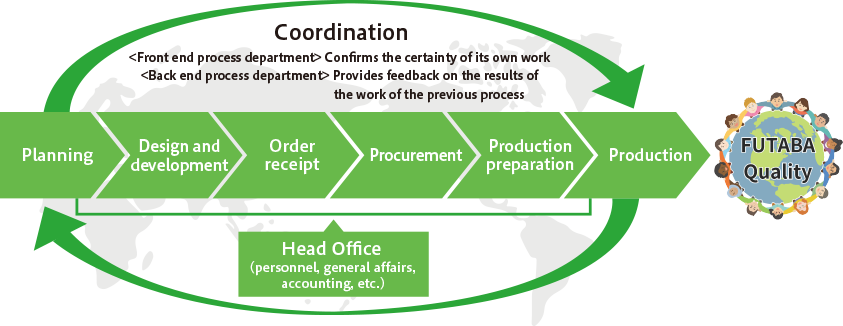
Quality improvement activities
We are conducting our daily activities to respond to the expectations of our customers, such as business quality improvement with TQM and quality control activity confirmation meetings at manufacturing plants. In addition, we are working to improve the quality of all of the Company's products by sharing issues and failure information as well as examples of improvements through meetings with suppliers. If quality issues arise, relevant departments within the Company cooperate to thoroughly investigate the cause and take measures to prevent recurrence. Top management also visits sites to confirm the accuracy of countermeasures, feedback to engineering, and production engineering divisions, and standardization.
Performing QA inspection
The Process Management Audit Department conducts QA inspections (quality assurance structure inspections and process inspections) at all plants in Japan and overseas. Any issues that emerge will be followed up on until improvements are completed, and confirmation will also be made regarding their deployment to other processes. In addition, strong initiatives are introduced at events such as quality function meetings and during Quality Month, part of company-wide efforts to elevate quality. We also conduct QA inspections of suppliers' processes and advance improvements.
Human resources development activities
Our training program inculcates knowledge of quality required for productization as well as understanding of the roles of manufacturing processes and quality assurance systems required for process assurance, and skills for prevention and recurrence prevention. Furthermore, quality assurance rule education enhances understanding of personal roles, responsibilities and the significance of work, thereby increasing satisfaction.
During the Global Quality Month in November every year, we raise the quality awareness of all employees and create a quality culture under the theme of "Know, Think, and Act on Futaba's Quality." In addition, we have been holding global quality brainstorming sessions since 2023, the launch of activities where quality divisions come together and brainstorm.